When using a laser cutting machine, a good cutting effect is also inseparable from the assistance of various gases. In addition to the laser pointer auxiliary gas purity requirements. There are also extremely high requirements for air pressure during the cutting process. During the laser cutting process, the auxiliary gas must have sufficient pressure to completely remove the waste residue generated by the cutting. Generally, when cutting a thicker workpiece, the air pressure should be reduced a little. The residue sticking to the workpiece will destroy the cutting edge. The popularity of laser cutting machines may not even be foreseen by the inventors. With the rapid development over the years, the industry has been constantly updated and upgraded. For the improvement of processing requirements, the operation requirements during the cutting process are becoming more and more detailed.
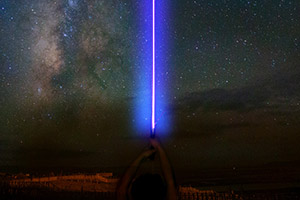
Increasing the gas pressure can advance the cutting speed. But after reaching a maximum value, continuing to increase the gas pressure will cause the cutting speed to decrease. Under the high auxiliary gas pressure, the reason for the reduction of the cutting speed can be attributed to the enhancement of the cooling effect of the high air flow rate and the action area. It may also be the interference of intermittent shock waves in the airflow on the cooling of the laser action area. Uneven pressure and temperature in the air flow will cause changes in the air flow field density. Such a density gradient causes the refractive index in the field to change, thereby focusing the energy of the green laser pointer beam. Cause refocusing or beam divergence. This interference will affect the melting efficiency and may sometimes change the mode structure. The cutting quality will be reduced if the beam diverges too much. Making the light spot too large may even cause serious consequences that the cutting cannot be performed effectively.