The choice of welding solution is a complex laser pointer problem for each application. Generally speaking, the greater the number of short welds. And distributed over a large area (such as doors, seat structures and body parts of automobile assemblies). Compared with fixed optical head welding, remote laser welding (RLW) also has greater advantages. The use of RLW technology shortens the processing cycle by up to 50%. The examples also cover high-density welding, precision welding, and large-scale structural welding with multiple welds. In particular, we can see that part of the weld of this part continues from the top plate to the bottom plate. This type of structure is not easy to implement using conventional welding heads for welding.
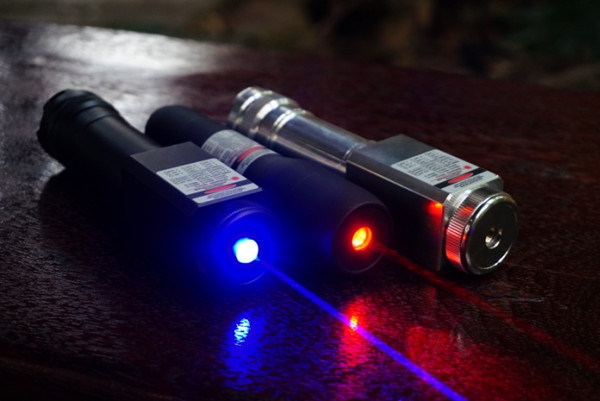
In addition, RLW can provide many advanced functions for welding process control. For example, if it is necessary to swing the welding point in the welding area. Or the processing process includes complex welding shapes, and the processing speed and accuracy of the scanning method will be better than the use of robots for small amplitude high-speed movements. The scanning speed of the RLW scanning head can reach 90 to 180m per minute, while the maximum speed of the traditional robot is only about 10m / min. When processing high thermal conductivity materials with high-brightness fiber lasers, it is best to use small light spots to maintain the stability of the welding holes, but this processing method may make the processing process too violent and produce a large amount of welding spatter. Experiments prove that the high-brightness laser cooperates with the high-speed positioning of the remote scanning head to significantly reduce welding spatter. This is achieved by ensuring the stability of the welding hole through the beam swing. When welding copper and aluminum, if the beam swing mode is not used, the welding spatter will be very serious. Once the high frequency oscillating beam is used, welding spatter will be reduced. In addition, the green laser pointer's original anti-high anti-technology is also indispensable in this application. By installing a protection device, the equipment is protected from the damage of the retroreflected light. When processing highly reflective metals such as copper and aluminum, retroreflected light is inevitable. Traditional lasers are due to their natural sensitivity to retroreflected light. May cause unstable processing and destructive automatic shutdown, or even scrap.