Unexpectedly. The laser pointer parameters, which are almost the same as those used for copper materials, can also be used for marking the upper and lower surfaces of uncoated borosilicate glass. This further supports the hypothesis that non-linear absorption is due to the influence of high-peak-power fiber lasers. Checking the scribe area, you can see that the "cracking" condition is very limited, with cracks <10μm and surface roughness <5μmRa. The underlined and non-cracked condition is shown under low magnification. The most interesting result of this process. Among them, the reflectivity of the glass surface can be tightly controlled by changing the scanning parameters.
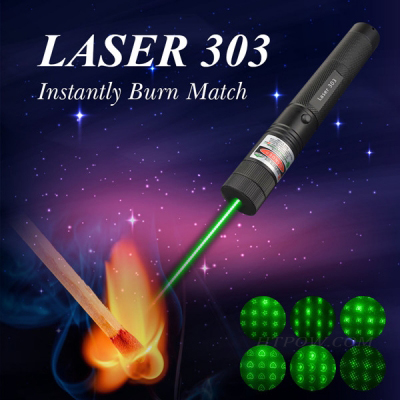
This article explores how to quantify laser marking and surface texturing. And use these technologies to laser mark aluminum. Techniques for marking more challenging copper and uncoated glass surfaces are shown. In the future, there will be process applications applicable to a wider range of surface structures.
green laser pointer welding between copper or other metals has always been a problem in the field of low-power heat conduction welding, because of the inherent high reflectivity and diffusion coefficient, and the inconsistent native surface oxide layer. It turns out that this dark marking technology can improve consistency when welding copper. As part of ongoing research. Laser beam to improve and regulate surface absorption. These fine structures can also improve the bond between copper or aluminum and other dissimilar metals.
Green is more sensitive to eyes than red. Even with the same output, the laser pointer feels brighter than the red one. See standard luminous efficiency curve. Green (532nm) is about 10 times more sensitive than red (780nm or 650nm). If the laser modules have high output, they can be dangerous when they enter your eyes. Therefore, the output power of laser pointers on the market is limited to about 1mW. The output power of this green laser pointer is very high, 5 to 30 mW.