Laser drilling is a technology that can produce holes with a high aspect ratio or a hole with a depth-to-diameter ratio far greater than 10:1. The high aspect ratio holes drilled by the laser can be used for a variety of purposes, such as cooling holes for aerospace turbine engines, oil passages in certain engine blocks, printed circuit board micro-holes and green laser pointer fusion components. It includes a pump source, a resonator mirror and a laser self-frequency-doubling crystal; the self-frequency-doubling crystal is processed along the frequency-doubling phase matching direction into a rectangular parallelepiped or cylinder, and its two end faces are transparent planes and parallel to each other; One of the transparent plane plating of the frequency doubling crystal is a dielectric film with high transmission for pump light, high reflection of the fundamental frequency light, and high reflection of the frequency doubling light as the input mirror; another transparent plane plating for partial transmission of the fundamental frequency light and high frequency doubling light The reflective dielectric film is used as the output mirror; the end-pumping method is as follows: a self-frequency doubling crystal is arranged in front of the output light of the pump source, and the end of the self-frequency doubling crystal coated with the input mirror faces the output light of the pump source Placement; the side pumping method is adopted: the pump source is set on the side of the self-frequency doubling crystal. The laser realizes the fundamental frequency light generation and the second harmonic process through a single self-frequency doubling crystal, and has the characteristics of simple operation, reliable performance, high output power and high stability.
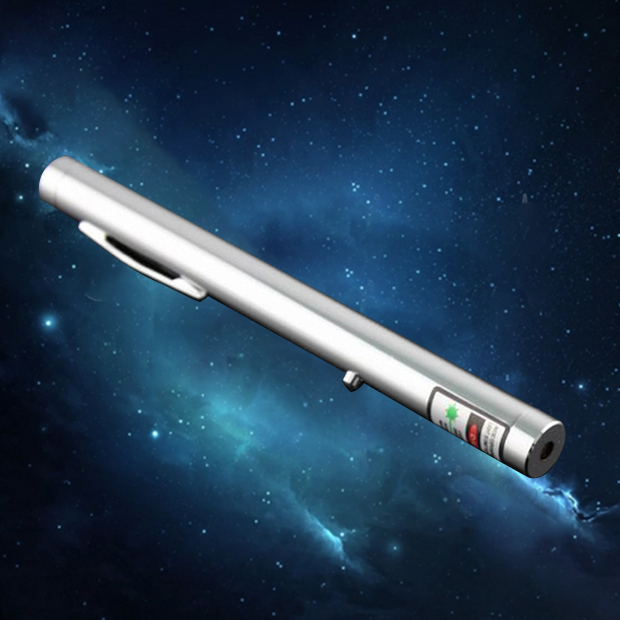
Manufacturers of turbine engines used for aircraft power generation and propulsion are very fond of using high powered laser to drill small (usually 15-90 mm diameter) cylindrical holes on the surface of metal sheets, castings and machined parts at a temperature of 0.3 to 1 degrees Celsius. 0.3°. Laser drilling can produce holes at a very shallow angle to the surface of the material, at a rate of 3 to XNUMX holes per second. This allows new designs that include film cooling holes to reduce noise, improve fuel efficiency, and reduce CO and NOx emissions.
The development of laser use and control technology processes has led to a significant increase in the number of cooling holes present in turbine engines. The increased use of laser drilling depends on many parameters, such as drilling quality and drilling speed.